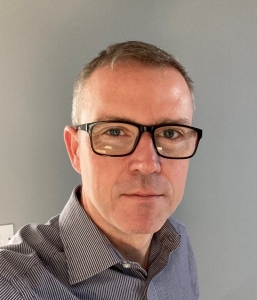
Opinion piece by David MaCGregor, Business Development Manager
Continuous Improvement (CI) is in my blood…. Well, that is maybe a little strong but I certainly look at many activities and naturally think how best can that be done. My thinking can be limited as I’m not a naturally creative person as has been borne out in a number of different profiling assessments I’ve completed through the years. I therefore pull on others much of the time, to help to get to the ‘better’ answer or solution. Clearly there is much more to it than that and it needs to be a process to first determine if we indeed do have a problem, a challenge or an opportunity. We must then articulate that quantifiably which can be a real challenge. Making improvements and seeing the benefits should be a great buzz and feeling for anyone - and in my experience, this has proved to be the case.
I was therefore taken aback when reading a recent news article which indicated that arguably the innovators of many Lean and CI thinking ways, means and methods are having a spot of bother, quite a serious spot of bother! One that you would imagine after so many years of honing their own techniques and dare I say Continuously Improving they would have an effective and efficient process for.
However, it seems not. Clearly no one is immune from either an internal issue or an external challenge, and in this case it would appear to be the latter. Perhaps no surprise but Toyota, like many competitors, are having some real concerns through their supply chain and have had to close some plants because of it, reporting that they expect to lose around 14,000 cars in December. The firm further reported that the stoppages were due to "lower attendance rate at suppliers in South East Asia due to the re-spread of Covid-19 and tight logistics situation in Japan."
Clearly out with their control you could argue, but this pandemic is not new. Previous supply chain challenges are not new, but it makes we me wonder if the Toyota CI team could have been a little more creative, or perhaps they have not been as engaging with their key supply chain partners as (their own) theory would suggest a business should be.
There is much to this story that is unknown but this is clearly a real problem for one of the leading global manufacturing organisations in the world and also leaders in the development of Lean Thinking and Continuous Improvement. We don’t know all the facts but this is certainly another warning sign to all manufacturing organisations that, while things out with our control can cause issues, we must be doing all we can to attempt to mitigate these. Ensuring we get even earlier warning signs through regular and meaningful engagement and speaking to our critical supply chains. We are, after all, one big supply chain and therefore we should be in external conversation all of the time which I’m sure we think we are, but perhaps we need to give this some extra thought and challenge ourselves to make sure we are doing all we can. Maybe, just maybe, there is an opportunity for improvement?
As a conclusion to this particular story, Toyota have stated that they aim to stick to their annual global production target for the year ending on 31st March: "We would like to maintain 9 million units, but we will keep a close eye on the situation."
This is perhaps proof that externally they are engaging, collaborating and continuously improving with their supply chain - and internally the Toyota CI team are in fact, rather reassuringly, still on it!