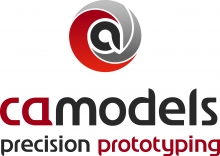
In the Spring of 1983, Clark Campbell finished his first order for a reputable product design company in the spare room of his flat. It was a hand-made presentation model in the form of a bright yellow underwater camera. The model was very well received by both the designer and customer. This was a defining moment for Clark – the realisation that he wanted to compete with the best model makers in the UK.
35 years on, CA Models is an established rapid prototyping, engineering and model making business. Industries including Formula 1, Aerospace, Defence, Oil and Gas, Medical Device and Product Design depend on CA Models for its market leading technology and craftsmanship, ensuring quality products and a responsive service. The 23,000 square foot factory is based in Scotland and has 30 staff members working in 11 departments, encompassing Additive Manufacturing (AM), CNC machining including 5 axis milling, turning and wire erosion, as well as Vacuum Casting, Model Shop, Painting and Specialist Finishing, Inspection, Scanning and CAD.
Whilst AM, also commonly referred to as 3D printing, has seen a popularity boom over the past decade, CA Models invested in its first machine over 20 years ago and the department has been evolving since. Stereolithography (SLA) is the largest and most popular of CA Models’ AM services. The department houses a broad range (nine machines) of the very latest SLA technology which can build almost anything from the smallest, most intricate, high-resolution parts with a layer thickness of 0.05mm, e.g. telephone keypad buttons, to large parts with 0.1mm layer thickness, maintaining outstanding surface smoothness with feature resolution and edge definition, e.g. 1:1 scale Formula 1 car gearboxes.
The latest and increasingly popular addition to CA Models’ AM service is the Metal AM department. This process allows components with geometries typically difficult or impossible to CNC machine, to be 3D printed from powdered aluminium or stainless steel. It also eliminates the need to go down the traditional foundry made castings route. CA Models bought their first metal AM machine in 2012. Their second, larger machine, the SLM 500HL arrived in January 2016.
After extensive research, development and collaboration with customers, CA Models now has the knowledge and experience required to achieve the best build, finish and optional post-machining, all in-house. CA Models’ unique ability to post-machine metal AM parts to tight tolerances, producing the highest quality finish, has become an invaluable pre-requisite for many customers.
CA Models other three AM departments include Selective Laser Sintering (SLS), Fused Deposition Modelling (FDM) and Connex multi-material polyjet 3D printing. The SLS department is often used to build strong, flexible, fully functional plastic products using nylon and carbon-filled materials, popular with product development and manufacturing.
The FDM department houses a Fortus 900 system suited to building fixtures, factory tooling and end-use parts in high-performance thermoplastic material for biocompatibility, static dissipation and resistance to heat and chemicals. Materials such as ABS, Ultem (flame retardant) and SR30 are available; the latter has proven very popular with customers requiring soluble cores and mandrels, ultimately speeding up the composite manufacturing process.
The Objet Connex 500 multi-material polyjet 3D printer enables simultaneous printing of multiple models in multiple materials on a single build tray which is beneficial for reducing production time. With a choice of up to 14 different materials, this method provides the customer with a prototype that has a realistic rendering of the final product.
Maintaining the quality and accuracy during the hand-finishing of AM parts is fundamental to CA Models’ reputation. This careful process is carried out in the Model Shop by one or more of the six craftsmen and model makers. Additionally, parts can be painted or powder coated to a flawless finish if required, in the large capacity industrial Paint Room.
CA Models’ CNC department boasts the latest in 5 axis milling, turning and wire erosion technology. The most recent purchase is a DMG Mori DMU 100 eVo linear milling machine. This impressive machine broadens CA Models’ capabilities further, benefiting customers who require a large envelope size and swift turn around.
The ability to complete the most challenging, specialist jobs successfully within a tight delivery schedule ensures that CA Models’ CNC department is constantly busy with large complex components, minute intricate parts and almost anything in between. The broad range of materials available include hard steels, alloys and plastics. Quantities generally range from one off to low volume batch production. The groundbreaking partnership between metal AM and CNC post-machining of 3D printed metal components, has without question become much in demand.
Many of the 30 staff members have been working with CA Models for over 15 years. From administration to management, manufacturing to manual labour, their enviable skill set and experience is instrumental throughout the production process.
The combined range of technologies and services on offer marks CA Models as a unique facility, the biggest and most capable of its kind. Customers have been returning for over 30 years with confidence that they will receive excellent service, the highest-quality products and within the shortest possible timescale.